

Scrubber dryer
Troubleshooting giude
Save downtime on your cleaning machine!
Make sure your machinery isn't left in the cleaning cupboard with our expert troubleshooting guide.
Regular cleaning and maintenance of your machine will improve the standard of cleaning, and maximise cleaning time and machine longevity.
These are expensive machines and all authorised users should be taught how to use their machine
we can offer this service face to face at our training facility, on your site or via videos).
First things first.
You should ALWAYS sweep or vacuum the area before you use a scrubber dryer.
Although all are fitted with debris filters, this is only for the bits you may have missed.
Use chemicals in accordance with your COSHH training (available through us if you need it) and do not use high foaming products in a scrubber dryer. Why? Because the foam can get past the clean water filter and get into the motor - wet and motors do not mix and this will invalidate warranty on any machine.
Every machine has an efficient cleaning speed. This gives the machine a good amount of time to lay the water and chemical on the floor and give a good scrub before the dirty water is picked up.
Driven models usually have this marked on the speed regulator.
For push along models, a slow steady pace gives the best results.
Machine not starting.
Is there a launch sequence for the machine?
Most have a specific way of starting the machine so that non authorised users cannot switch them on. This may be as simple as pulling the triggers and releasing before starting.
Battery machines.
Check that the machine is started with a key or battery isolation switch.
Are the batteries charged?
Usually there is a light on the charger to indicate charging and when the cycle is complete.
Are the batteries connected?
If batteries are removeable, are they in and fitting snuggly?
For non-removeable batteries, you can often find the batteries under the removeable top tank. These have a fuse on them and most machines come with spare fuses (quite rare for these to go).
Mains Machines.
Is it plugged in and switched on?
An obvious one, but always worth double checking. Most machines have a light to indicate the power is reaching the machine.
Most machines use are fairly high wattage, so check the fuse in the plug. If they are being used on an extension lead, try without the lead to check for that issue.
A special one for 110V machines plugged into a transformer. Most standard transformers with 2 x 16A outlets are designed for use with power tools. These transformers are usually only rated for 5 minutes of continuous use, before they switch off for 10-15 mins. Check that your transformer is suitable for continuous use -it will state this. Most transformers with 32A (large size) outlets are designated for use.
**Good practice when you have finished with the machine. Wind the cable starting from the machine end, and wipe with a dry cloth as you go. You can then feel the cable for kinks and cuts - often caused by being trapped in doors etc. Any kinks should be examined for damage, and if you find any cuts stop using the machine and replace the cable**
No water on the floor
Starting with the obvious - is there water in the machine? If there is but the water level is very low this could stop the flow.
Most machines have a flow control lever or tap (or two in some cases).
If there is an airlock, turning the lever to maximum and running the machine will usually clear this and will restart the water. Then reset the lever to the desired flow rate depending on floor type and how fast you walk.
Airlocks can be quite common, for example running the water to empty then refilling can cause this.
Has the machine been left for a long time with clean water & chemical left in it?
Best practice is to empty the machine of both dirty and clean water tanks after every use.
If the machine has been left unused for a few weeks - for example over school holidays - the chemical can jellify. Machines have a filter in the clean tank where the water is released, or externally - these can be removed and cleaned under a tap.
Not picking up
Switch the vacuum on - this can be done independently of using the machine. Can you hear the motor? If not, jump to machine not starting, or give us a call.
Is the dirty water tank full? All machines have a cut-off to stop overflowing.
The separator assembly usually sits on top of the dirty tank, and has 2 hoses going into it.
This has a seal that needs to be intact to create suction. Check its there, and not twisted or crimped.
Pull one of the hoses out (doesn't matter which, but only one at a time to avoid mixing them up when reconnecting). Turn the vacuum on, and check the end of the hose for suction. If you have it, then this hose leads directly to the motor, and the motor is working as it should. Replace this hose, and focus on the other one.
Take the other hose out of the separator, and check the suction at the point on the assembly where you removed it. If there is no suction here then there is a blockage in the assembly, usually where the debris filter is. Remove the whole assembly and clean thoroughly. Replace and check again. Ensure hoses are returned to the same side they were removed from.
The other end of the second hose attaches to the floor squeegee. With this put back in the separator assembly, turn the vacuum on again. Check the end of the hose this time for suction. If there is none, there is a blockage in this pipe. Remove the pipe and remove the blockage. Tip - use a coin and run through the pipe - this will show a blockage straight away.
If the suction is there but weak, it could be a part blockage or a hole in the hose - check both.
The last thing to list, although maybe the first to check, is the floor tool squeegee itself. These can get blocked at the joint to the hose or if there is a bend in them - the Numatic 1840 machines even have a removeable cap to clean them out.
**Was it a blockage? Make sure you vacuum or sweep the floor before you use your machine!**

Separator Assembly
General poor results
Leaving streaks on the floor
The main cause of this is debris in the squeegee blades. Ensure you vacuum or sweep the area before using your machine. Lift the squeegee assembly and wipe with a clean cloth, then carry on.
Check the blades for signs of wear, and replace if necessary.
If the streaks are on one side only, check the floor tool is attached properly and flat to the ground - some machines have an adjustment for this.
Not cleaning the floor properly
Check the chemical you are using is suitable for the contamination you are trying to pick up, and check the dilution levels are correct. Also ensure the correct use of brushes / pads - see further down.
Leaving a puddle behind at the end
This generally happens when the vacuum is switched off too quickly. Let them run for 20-30 seconds after you have finished, to make sure the hoses are all clear.
Most machines have hose retaining clips close to the floor tool - similar to your washing machine at home. Fit the hose straight down from the machine, into the clip, then up through the next clip and down onto the floor tool - close to a figure of 8 shape.
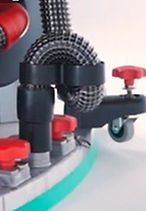
Hose fitting
© 2021 Cotton & Sons Cleaning Supplies Ltd. All Rights Reserved.